Citi-Con’s concrete knowledge successfully deployed on new landmark development
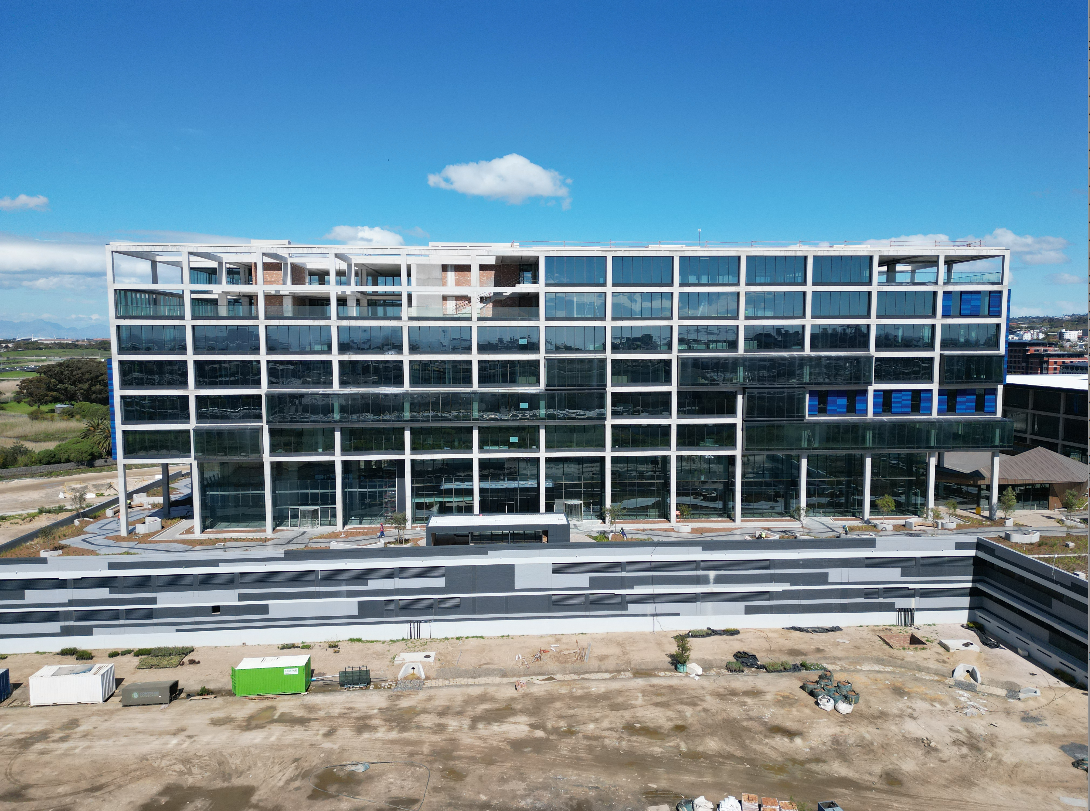
16-07-2024
Read : 149 times
The Content Engine
Source
The extensive skills and experience of concrete repair specialist, Citi-Con, were successfully harnessed to solve abnormal discolouring of exposed concrete of the new 38 000m2 Amazon head office in Precinct 2 of the R4-billion River Club mixed-used development. Notably, Citi-Con finalised a project that should have taken three months to do so in only two months.
Working closely with architect, Paragon Architects, WBHO, the principal contractor; and StonCor Africa, a leading supplier of asset repair and maintenance systems, Citi-Con designed a system that would remove the efflorescence. Importantly, this had to be done in an extremely short timeframe to avoid delaying the opening of the building to its tenant.
The repair method was tested on various sample areas and approved by Paragon Architects. “It was not only effective, but also practical and feasible – among the other important considerations for a successful concrete repair method. Bear in mind that our operations coincided with the various specialist trades which were completing the final aspects of the build,” Andre Vermeulen, Managing Director of CitiCon, says.
About 8 000m2 of exposed concrete was significantly stained. This included the full length of the entire concrete beam around the perimeter of the building. There, the efflorescence was so severe that it had to be removed by grinding off a thin layer of concrete. Other areas were washed by hand with a weak-acid solution cleaner.
The concrete was then sealed with StonCor’s Pro-Struct 670. Pro-Struct 670 is a modified siloxane solubilised in aliphatic hydrocarbon for deep penetration in concrete substrates. This system is very effective in resisting water and salts that are normally encountered in natural-weathering conditions.
As an approved StonCor applicator, Citi-Con has extensive experience working with the product. This also means that the company can guarantee its workmanship for the maximum available term. It is very important considering since the leading cause of concrete repair failures is shoddy workmanship, including the incorrect use of repair systems.
The substrate was first thoroughly cleaned to remove all dirt and loose particles. Pro-Struct 670 was then applied to a dry surface with a low-pressure spray. As per StonCor’s instructions, the surface areas were flooded with the solution, with Citi-Con’s team ensuring a run-down on the masonry of between 150mm and 200mm. To avoid a high spread rate that would greatly reduce Pro-Struct 670’s effectiveness as a water repellent, a litre was used for every 2m2 to 4m2. This was dependent on the irregularities of the substrate surface.
Two coats of Pro-Struct 670 were applied with the second placed after about six hours and then allowed to cure over seven days.
Before the concrete could be sealed in this way, all of the windows had to be masked to avoid permanently staining them. This was an extensive undertaking that entailed covering 8 500m2 of glass within the vicinity of the various working areas.
Moreover, various areas of the building had to be prepared simultaneously. This is so that the programme could continue when the Citi-Con team was unable to work between the two towers due to very high wind speeds. Considering Cape Town’s “micro-climate” that presented new and unforeseen safety risks almost on a daily basis, Citi-Con had to adapt its programme regularly. This was done while working closely with WBHO to ensure minimal impact on the final aspects of the build.
Accessing the various work faces was a significant challenge. Initially, Citi-Con intended undertaking the entire project with rope access. This is considering that it is a quicker, more cost-effective and safer method of working at height, doing away with the need to erect scaffolding.
However, the building’s many overhangs obstructed the rope technicians. They were, therefore, equipped with window-suction cups to pull themselves closer to the working areas. While effective, it was a slow and tedious process. Thus, Citi-Con also deployed suspended cable systems and mobile scaffolding towers that could be easily moved around the perimeter of the building to the worksite. Adjusting them to the site elevations, the mobile scaffold towers provided safe and quick access to the fourth-floor level, 13 Citi-Con team members worked on this project. Among them were the company’s certified rope-access technicians. By bolstering the team and incorporating various innovative work-at-height methods into the programme, the company was able to finalise the scope of work a few days before the “builder’s holiday”, saving the client in both construction time and costs.
Impeccable health and safety practices were implemented on this project. Integrated health and safety specialist, KBC Health and Safety, was employed to assess and manage occupational health and safety risks on behalf of Citi-Con. Throughout the project, Citi-Con’s own robust occupational health and safety practices were in line with those of WBHO. The principal contractors’ own “zero harm” policy extends beyond its own operations to all its project stakeholders.
Upholding these high health and safety standards was also facilitated by a team that is very skilled and experienced working at height. Many of them have been with Citi-Con for more than 10 years, during which time they have received ongoing training to develop, hone and refine their skills. This includes regular health and safety training, which also involves revisiting the “basics”.
Vermeulen concludes by noting that he is very proud of his team’s performance on this project. “We have again demonstrated why we are the preferred provider of building revamp services. Together with a guarantee of quality workmanship performed by professionals, we provide an efficient, practical, cost-effective and safe method of repairing new and existing concrete,” he says.
For more information contact:
David Poggiolini
Debbie Poggiolini
Recent News
Here are recent news articles from the Building and Construction Industry.
Have you signed up for your free copy yet?